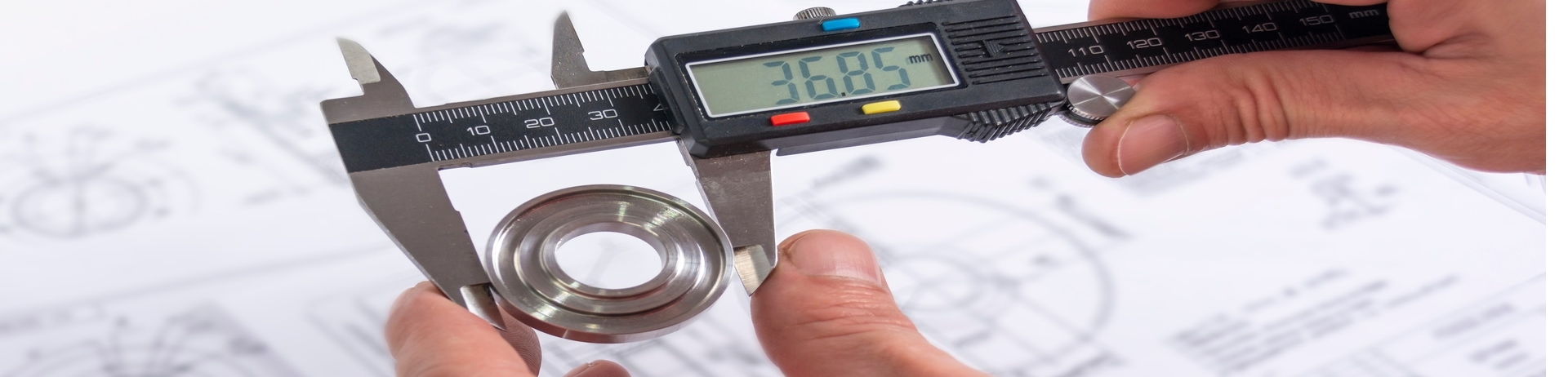
Initial Production Check
Case Study - Quality Control in Wooden Products before Shipped from Guangdong
Third Party Inspection
During the product inspection, firstly, we found that the small metallic accessories on the wooden blocks showed a 20% rusting rate. These metal components, lacking special treatment, rusted due to the moisture content in the wooden blocks. This problem affects the product's appearance in the short term and could worsen over time, especially considering the additional time the goods would spend in transit via sea before reaching the customer.
Secondly, we found the assembly testing of wooden strips revealed a critical issue. The factory neglected the proper sizing of the wooden strips, making correct assembly impossible. Despite the factory suggesting that greater force could resolve the issue, even with considerable effort, a worker managed to assemble one product, leaving the bottom of the wooden strips heavily abraded. Initially, the factory hesitated to acknowledge the severity of the problem, insisting that it merely required more force. However, after several attempts, they finally admitted the issue's gravity, recognizing the substantial force required, making it nearly impossible for an average person.
In addition to these problems, the inspection uncovered an infestation of insects, marking the inspector's first encounter with such an issue. The factory justified this by claiming it's inevitable with wooden products. However, per export standards, insects constitute a critical and unacceptable problem.
The factory seemed to lack a mature quality management system. Planning to export the products directly upon their return from Guangxi, it was fortunate that the customer arranged for a third-party inspection; otherwise, they would have received a batch of unusable wooden pieces.
In addressing these issues, our inspection service played a crucial role. We not only helped the customer identify hidden quality problems but also provided professional advice and solutions once the problems were exposed.
By promptly identifying problems and offering solutions, our company assisted the customer in avoiding potential economic losses. We are dedicated to working closely with our clients, ensuring they receive high-quality products meeting market standards, and minimizing the risk of any potential claims.
- Cost-effectiveness of Third-party Inspection Services
- Quality Control Audit
- Case Study - Quality Control in Wooden Products before Shipped from Guangdong
- Manufacturing Inspection
- Case Study - Mold on Nail Files found from the product inspection
- Production Inspection in Vietnam: Why Hire Third-Party Inspection?
- Case Study - Unveiling Barcode Mishaps
- Factory Inspection