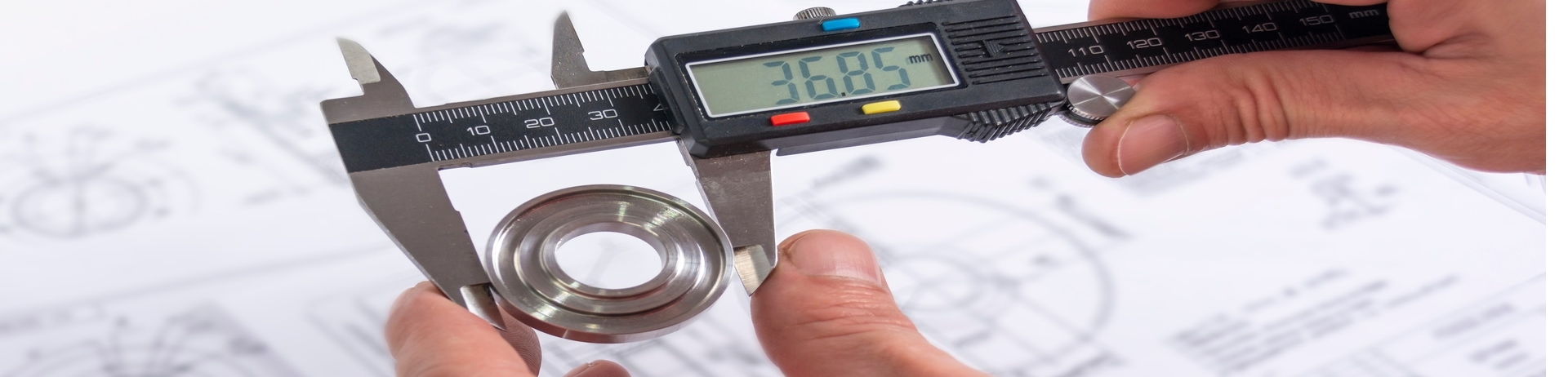
Initial Production Check
Case Study - Manufacturing Discrepancy in Pet Ladders
Asia quality control
In this case, we dealt with a quality inspection of pet ladders. This product is designed to be assembled from multiple components due to transportation requirements (photo 2). On that particular day, various products were undergoing inspection, and we conducted assembly tests for each of them.
While assembling this specific product, we discovered that the dimensions of the bottom groove and the insert plate didn't match.
The groove size was smaller than the insert plate size, preventing the insert plate from fitting correctly and hindering proper assembly (photo 3&4&5). We repeated the assembly with another set of products from the factory and encountered the same issue. Upon checking the sampled products, we found this problem was consistent across the entire batch.
This issue exposed a manufacturing process in which the factory merely followed design data without accounting for potential errors arising from various production phases or deviations due to material and environmental factors. The factory acknowledged this oversight and appreciated our assistance in identifying the problem.
Had this issue reached the hands of consumers, it would undoubtedly lead to product returns. Through professional inspection services, we can identify and rectify such issues before the product reaches the market, ensuring that it meets high-quality standards and upholds customer trust and satisfaction.
- Cost-effectiveness of Third-party Inspection Services
- Case Study - Quality Control in Wooden Products before Shipped from Guangdong
- How Our Quality Control Audits Benefit Your Firm
- Production Inspection in Vietnam: Why Hire Third-Party Inspection?
- Case Study - Mold on Nail Files found from the product inspection
- Sit Back and Relax with HKQC Center Quality Check Services
- supply chain audit post
- Case Study - Revealing Potential Hazards through Product Inspection: Safety Concerns in Everyday Products