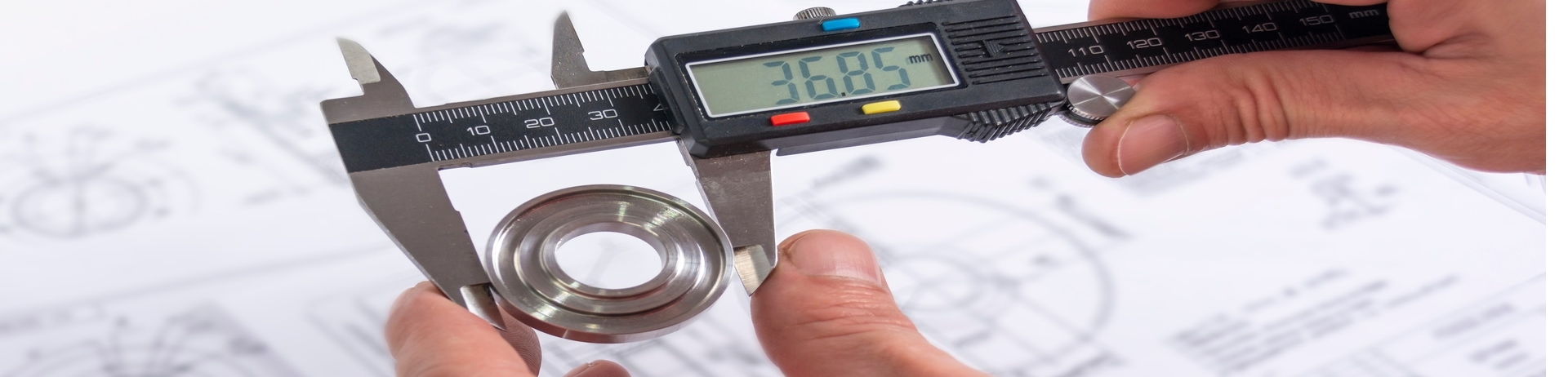
Initial Production Check
Case Study - A Lesson in Bamboo Fencing Inspection
Asia quality control
This case describes our experience in the reinspection of bamboo used for weaving fences.
In the previous inspection, the bamboo was heavily affected by pest damage and breakage, falling short of the required quality standards. Consequently, the factory decided to prepare a new batch of bamboo. However, the factory's inspection environment was quite challenging, lacking furniture such as tables and chairs. As a result, the inspection had to be conducted on a piece of cloth laid out on the muddy ground. With a considerable quantity of bamboo to inspect, some pieces reaching lengths of 2 to 3 meters, our inspector worked on extracting samples while the factory's supervisor remained present, repeatedly referencing the previous inspection report. The supervisor asserted that the previous report had unfairly characterized their bamboo, leading to shipment delays. He claimed that this time, they had prepared a superior batch.
Our inspector clarified that the previous inspection had followed standard procedures and emphasized the need for an honest assessment. He also reminded the supervisor that he had signed off on the previous inspection report. As the inspection continued, our inspector had to crouch down to examine the bamboo closely due to the adverse conditions. Meanwhile, the factory's supervisor was actively assisting by passing bamboo pieces for inspection, one by one. However, our inspector began to sense something was amiss. Each bamboo piece appeared to be in perfect condition, and no issues resembling those from the previous inspection were found. Suspicion grew that the supervisor might have selectively screened the bamboo before handing it over, discreetly disposing of the damaged pieces and only presenting the intact ones. Our inspector immediately intervened, clearly explaining the inspection protocols and warning the supervisor that any attempts at deception would be reported accurately to our company and the client.
Subsequently, our inspector reorganized the samples, placing them within his direct line of sight. He meticulously examined each piece, ensuring there is no affection of the supervisor or factory workers, in order to perform integrity and honesty of the inspection process. This case underscores the importance of awareness in inspections, ensuring that customers receive high-quality products. It also serves as a reminder to our factory partners that adhering to inspection rules is crucial for maintaining the integrity and reliability of the supply chain.
- Case Study - Ensuring Product Safety in Plush Toys: A Critical Quality Intervention
- Production Inspection in Vietnam: Why Hire Third-Party Inspection?
- Case Study - Mold on Nail Files found from the product inspection
- Case Study - Discovered Hangtag Print Residue during Pre-shipment Inspection
- Case Study - Attention to Detail and Product Integrity - Hook Design Oversight
- Case Study - Attention to Detail - Snap Button Issue in Skiwear Accessories
- Case Study - Quality Implications of a Pet Chew Toy with Sound Function
- Case Study - Decisive Differences in Barcodes and Model Numbers