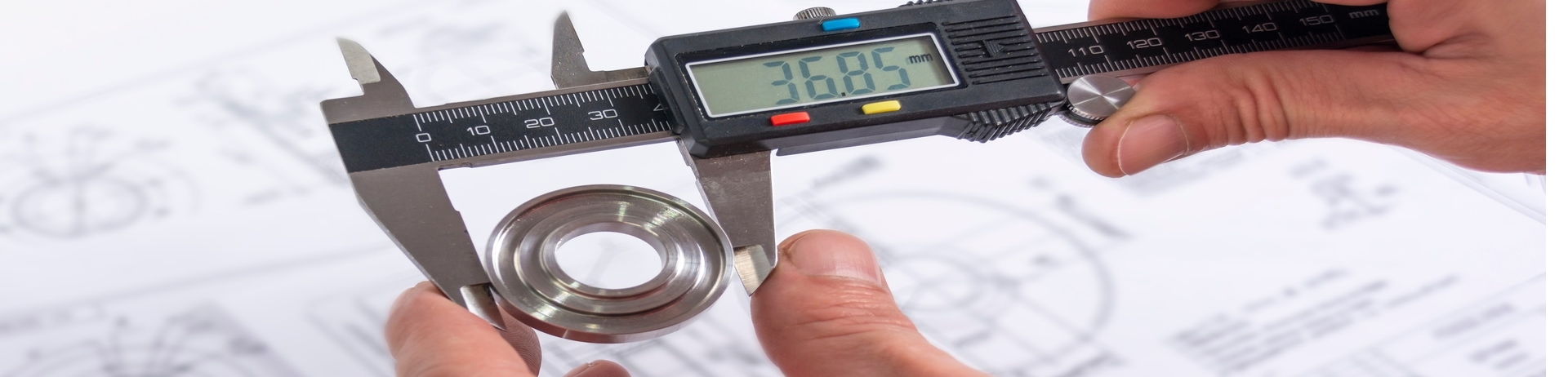
Initial Production Check
Case Study - Unveiling Barcode Mishaps
Third Party Inspection
During a recent inspection, as we proceeded with barcode scanning tests, a factory assistant unexpectedly volunteered their own barcode scanner, offering to help. Though our inspection team declined the assistance, we inquired about their intentions. Their explanation was that they wanted to test a newly acquired scanner. Politely declining, we assured them of our capability to carry out the standard procedure. Following this, our inspector performed the scans, only to discover a discrepancy (photo1) in the barcode on one product's outer box (photo2). After several attempts, the issue persisted. The factory explained it might be a printing error, and our inspector proposed noting this for the client.
However, the factory assistant quickly reported this to their higher-ups, who then engaged in a discussion with our inspector. They asked if the issue could be omitted from the report. Our inspector insisted on transparency and questioned the rationale. The factory attributed the problem was due to incorrect client-provided data, subsequently updated. They explained that the external barcode had been altered, but its internal content remained unchanged due to a mishap at the box manufacturer. Recognizing the seriousness, the factory committed to replacing the boxes and resolving the issue. Despite their plea to omit the details from the report, our inspector held firm.
Our role as an inspection company is to ensure accurate documentation and advocate for product quality. In situations like these, our vigilance prevents potential issues from being concealed. We prioritize client interests, safeguarding them from unanticipated product problems and fostering supplier accountability. This case underscores our commitment to thorough and unbiased reporting, ultimately empowering clients with the information they need to make informed decisions.
- Case Study - Attention to Detail and Product Integrity - Hook Design Oversight
- Electronic Inspection
- Case Study - Unveiling Hidden Printing Errors: How Vigilant Quality Control Enhances Product Integrity
- supply chain audit post
- Case Study - Mold on Nail Files found from the product inspection
- How Product Inspection Can Be Benefitting In Every Way?
- Case Study - Decisive Differences in Barcodes and Model Numbers
- Case Study - Vigilance and Swift Detection: Fake Cartons Incident